Hot Products
Our premier offerings include the Intelligent Visual Line Drawing Machine, the Laser&Vibrating-knife Cutting Machine and the Non-sewing Laminating Machine for Shoe-uppers.
About Chuanya
Established in 2018, Quanzhou Chuanya Machinery Equipment Co., Ltd.
(Chuanya Machinery) is a certified high-tech enterprise based in China, specializing
in the development, manufacturing and sales of cutting-edge shoe-making machinery.
Our premier offerings include the Intelligent Visual Line Drawing Machine, the
Laser&Vibrating-knife Cutting Machine and the Non-sewing Laminating Machine for
Shoe-uppers
Production experience
An annual output
Shoe machinery
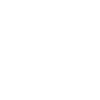
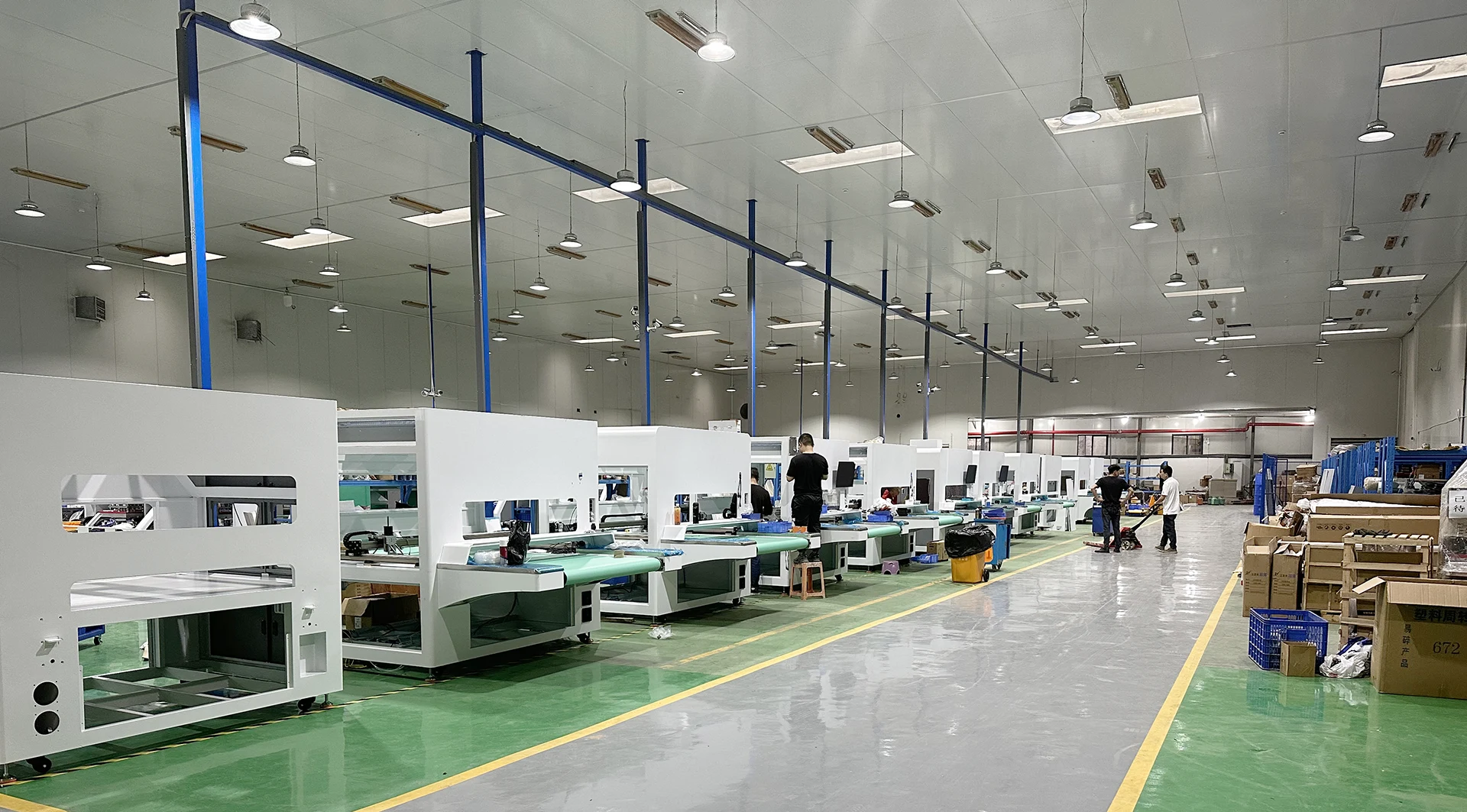
Let's hold hands to create a brilliant future!
Our Advantages
Our products are designed with integrated human-machine interface, achieving intelligent troubleshooting and simplified operation, which are highly supported and favored by numerous customers. Our intelligent visual line drawing machines, laser & vibration knife cutting machines, and other equipment are leading products in the industry, providing strong support for the intelligent manufacturing upgrade of the footwear industry.
Innovation
With our independent core R&D team, we continuously innovate and upgrade our products to meet the evolving needs of our customers, contributing to the intelligent manufacturing upgrade of the footwear industry.
Quality Assurance
Our products have passed numerous domestic and international certifications, including ISO certification and CE certification, etc. to ensure that each equipment meets the highest industrystandards.
Customization Service for Customers
We have a professional technical team that can tailor machines and solutions to the specific needs and requirements of our customers, ensuring a perfect match for their production demands.
Our Commitment
Chuanya Machinery has always adhered to the philosophy of "Customer-focused, Technology-Core," committed to providing customers with efficient, energy-saving,
environmentally friendly, and intelligent footwear solutions.
Our Vision
We are committed to building a technology-driven machinery company with warmth, speed, and altitude. By cultivating new productivity with high quality and integrity, we will fulfill our social responsibilities with our original mission at heart.
News & Blog
Meets multiple quality standards both domestically and internationally